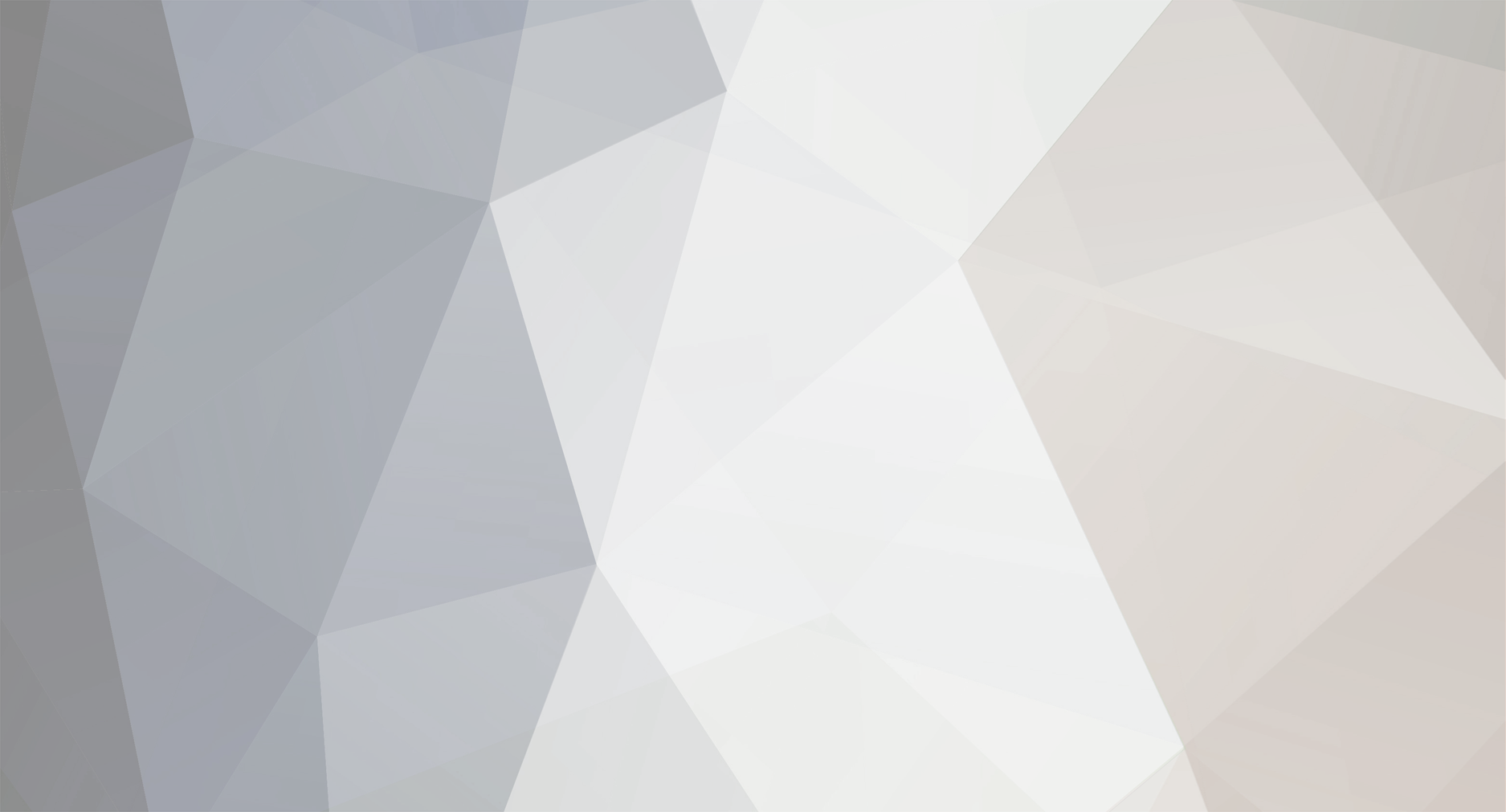
rpllib
Free Member-
Posts
66 -
Joined
-
Last visited
-
Days Won
20
Content Type
Forums
AutoShopOwner Articles
Downloads
Blogs
Gallery
Profiles
Events
Store
Links Directory
Shop Labor Rates
Community Map
Everything posted by rpllib
-
The following are posts I made on the AOCA website outlining an issue(potential nightmare) we had on 2017 Chevrolet Colorado: Randy_Lucyk Joined: Dec 21, 2011 Total Posts: 83 Feb 8, 2018 3:03 PM Unfortunately, I believe this is exactly what this may turn into for shops and consumers. We recently had a report of an oil filter failure on a 2017 Chevrolet Colorado with 13304 miles on the truck and the issue occurred 400 miles after our oil change. Customer had a check engine light come on so he headed right off to the dealer to have it checked under warranty. It had a VVT code stored and the dealer started looking into the issue. They found the filter failure and sent a picture of the image off to the customer. We used a Performax P0171 filter. The customer sent me the attached image of the obviously failed filter. I am immediately highly concerned, but the dealer is being unusually understanding of the failure. We spend some time with the service manager and find out that their appears to be an issue starting to show up on these vehicles, where the stand pipe in the filter housing is coming off with the old filter and being disposed of without the techs knowledge. We had great video of the oil change and their was nothing visible with the old filter as it was removed. The premises is that without the standpipes restricting/diverting functionality in place, full oil flow is blowing out the filter and the everything flows right down the filter housing port into the cylinder heads and remainder of the motor and plugs up components and passages. We asked for a picture of the filter housing and received image 2 attached. This appears that it may be a problem starting in 17 model year, but i can't be sure of that yet. I am digging for additional info now and will update as more information becomes available. Randy_Lucyk Joined: Dec 21, 2011 Total Posts: 83 Feb 9, 2018 7:59 AM This appears to be both a GM issue and a in-shop issue. Now that I see the notification GM released last week, i believe this issue occurred at the original oil change prior to the one we did. As I said, we had great video of the open end of the old filter as we removed it from the vehicle and I don't believe this stand pipe could have possibly been inside. Their is also no evidence of the tech struggling with anything "down in there" other then the normal A/C line interference issue. . Looking at the design and the A/C line interference, I suspect that the stand pipe is being knocked loose as the filter is being "angled" around the A/C lines to get the old one out. I suspect the oring on the stand pipe is the only thing holding it in the oil filter housing. Once the standpipe is disposed of, the housing has to be replaced, as the stand pipe is not available separately. The housings are in short supply with only three left in the country on dealers shelves and none in Gm distribution centers. Their is a new part number for the housing and those are not available yet. Original pt# 12675707 and new pt# 12682014. Looking at the attached illustrations and notice, it would not be easy to completely miss the fact that a problem was evident. The stand pipe looks too big to me to be easily missed. I suspect it is plastic and the words "housing cracked" was mentioned in the conversation with the service manager. I wonder if the stand pipe is actually cracking during removal of the filter, making it difficult/impossible to reinstall. If we did not do it, then why the old filter had not failed yet ours did, comes into question. Cold weather "full oil flow" was also mentioned in the conversation with the service manager, and those were the conditions at the time of the failure. The images also create some questions for me. The new housing does not appear to be identical to the OE installed housing, so is it an already redesigned housing? The filter bulletin in the Napa/Wix box talks about an update to the filter to include a check valve in the top of the filter. Our old filter does not appear to have this check valve, the Napa/Wix does and our new stock P0171 filters also have it. Looking at the design of the stand pipe in the new housing, it would almost appear that the small nipple on the end of the stand pipe might make more sense if it fit into the open hole of the old filter. The stand pipe design almost seems wrong for the filter with the check valve, unless it is shorter than it looks and never reaches the upper end of the filter. Would be great if the next shop to have one of these off would post some additional pics to try and help reduce confusion. Based on the notice from Gm, this does indeed look like it could get ugly. Although, this dealer covered all the extensive engine repairs under warranty(heads pulled, all new timing components, cleaning passages), i am not convinced all dealers will take that approach. In my case, it was nice(incredible?) to see GM step up and take responsibility. It helped that my customer (owner of the Colorado) retired from a GM primary supplier dealing with issues exactly like this for the later half of his career. He knew the right people to call to get the info needed to drill down to the root cause. Randy Lucyk Midas Kalkaska
-
I only know that they are (were?)in many Big O tire stores. My memory is that TBC was trying to get a new SMS system off the ground several years ago to entice Big O franchisees to use a new inhouse program.
-
WHY DO SOME SHOPS LIKE TO BAD MOUTH OTHER SHOPS
rpllib replied to xrac's topic in Dealing With Competition
Imo, this statement is the key to improving our image and customer perception(well done): " I proceeded to call the shop where the worked was performed and had them fax me a copy of the paperwork so I would be prepared when they came in." It is absolutely part of our job as professionals to call other shops and get the full story and backup documentation in a presumed warranty situation. When this industry gets in trouble is when we think it is OK to go ahead and do the work the "right way", charge the customer and then throw it back in the customers lap to deal with the previous shop on a presumed warranty situation. -
I might caution that not all labor law attorneys agree that flat rate technicians working in a non dealer environment are exempt from overtime. It appears there may be some variance among jurisdictions. It appears that most labor law attorneys agree that flat rate is an exempt form of pay in a dealership or other entity where new vehicles or equipment is sold as the primary business.
-
I am not known for being kind when it comes to this kind of stuff. The first guys are crooks and it goes without saying, they belong in prison. Real honest to goodness prison. If it was at my shop, i would call the BAR and in no uncertain terms demand immediate action and i would not let it go. If you have a bar, turn them in. If you let it out of your store without fixing, and/or left other brake lines on the vehicle that look just like the two that were leaking, I will turn You in, if there is such thing as a BAR in your state. Ladies and gentlemen, this insanity has to stop. Are we really replacing one rusty brake line at a time and putting these cars back on the same road my wife, children and grandchildren travel on. Are we really??? Really?? is that insane or what. Do we actually believe that the other brake lines are not at least worth a surge test in an attempt to verify their integrity, really?? Some one put one on a month ago, your putting one on today and we are going to continue this practice until someone gets killed or seriously injured. What a poor example we are setting. Not to worry though, it appears three months home confinement is what you get for taking taking a life due to incompetence and negligence. What a poor reflection that decision was on the great state of Vermont. Imagine being the family of the individual killed by this mechanic. Maybe it would be different if it was your mother. This lady died as a result of a rusted brake line failure. BARRE, Vt. - A Vermont mechanic originally charged with manslaughter for a faulty motor vehicle inspection has pleaded guilty to lesser charges. Steven Jalbert of Barre was arrested last August in connection with a 2014 crash that killed Elizabeth Ibey, 82. Prosecutors say the accident resulted from rusted out brake lines, despite the fact the car had recently passed a state inspection, performed by Jalbert. Last week, Jalbert accepted a plea deal for reckless endangerment and was sentenced to three months of home confinement. The attorney general's office says this was the first criminal prosecution in Vermont arising from a faulty motor vehicle inspection. We turn down at least one rusted and leaking brake line job a month because the customer believes they are better equipped to decide what needs to be replaced to insure safe brakes. Fix it right or don't fix it at all, period. Surge tests are a recognized form of brake line integrity test approved by many states with mandatory inspections. (Vehicle idling, your biggest gorilla technician jumping down on the brake pedal as if YOUR child just ran out from between parked cars) We can do better as an industry, I have no doubt
-
Something this thread has left me unclear of. Was the tech in question doing daily tracking of his productivity, which is different then the manager or owner doing it. If we have an expectation of our techs, do they know what it is and how they are measuring up, every single day. I don't hold much back from my staff. My line techs understand that we work for a 70% gross profit margin, or better, on there labor. Techs tracker allows them to see their gross pay calculate every day against what we should be paying them based on the gp% goal we have set for them. Pretty basic excel spread sheet that they fill out everyday. We saw a marked improvement in technicians buy in/understanding, when we implemented this in 2012. It's not a fixall, but it is an ingrediant.
-
Thanks Scott I appreciate the feedback. I have always had this dream of a "self spawning habit builder". The current IFTTT (if this then that) technology seems to have the potential, If we can use it with our SMS platforms and other digital assets we use daily. Can you envision Sharepoint integrating personally with your staff and bringing them around to actions that are the best use of their time and/or drives them down a SOP pathway when appropriate? Thanks Again for the engagement
-
Thanks Scott Waywedo also came up in my research. I have looked at sharepoint previously, certainly a fairly complete product. Can you tell me how many users you expect to have? That's part of the issue with these solutions, they charge by user. If I have a staff of 10, do i need 10 licenses. I would really like to get my folks involved in this process, so it has has to be fairly intuitive. I have set up many versions of some aspect of this in the past and the process or my execution of the process with my team failed. Probably the later. Thanks for the reply
-
Has anyone successfully moved to a sop platform like Process Street, Sweet Process, Pipfy or any other. It is time to bring our SOP's into something where they are easier to apply, self spawn, remind, and actually live in a fluid environment. SOP folder trees with word documents on our desktop just don't cut it anymore. I am looking to integrate process's with a calendar and ideally text reminders as well as tracking completions for repeating tasks. Any input is appreciated Randy
-
Almost done with ATI
rpllib replied to Bob K's topic in Management Coaching, Business Training, Consulting
Bob I have some experience in what you are finding with reduced car count due to running your business properly. We started down this road 15 years ago in a market that ranks 2.5 times lower potential then yours. Interestingly, two people on this thread commented on the markets they do business in, one from each end of the scale. Bob, you are from one of the lowest potential markets I have measured out of 1500 or so markets and mspec is from one of the highest potential markets. Curious how we all have similar challenges yet the solutions may require a somewhat different approach. In Bob's case, the outcome should have been completely predictable by ATI. It would not have been so obvious to ATI if the were thinking that Bob's market is the same as mspec's, and everything works the same regardless of the retail setting the shop is in. In mpsec's case, from my point of view, I would be happy to have my competitors be as backwards as possible, because their is a minimum level that many customers are willing to deal with, and the ones I consider higher value understand that it costs more to offer more. That is not to say that mpsec doesn't have an incredible amount of competition, like i can't even fathom, but i suspect his real competitors are organizations similar to his in offering, of which there are likely more than enough. If i have a challenge with training organizations, it is that they refuse to actively use accurate market potential to improve the outcome for their clients. They don't have to break it down to 100 different market segments, but their are 3 or 4 market levels that could make a difference if these organizations would use and understand them. Their coaches are no different than any of us, they know the market they came from and learn about nuances of other markets from us, while we pay them. Once you been around a lot of multi store owners with 20, 40, 60 or even 100 locations, you quickly learn that what works well long term in one market may not be so effective in others. Same owners, operationally similar process, same 8 bay facilities with sales ranging from 350k to 2.5m a year. There must be something with the market that causes that kind of range Randy Midas, Kalkaska -
What is your primary challenge ?
rpllib replied to Shopcat's topic in Business Talk - How's your shop doing?
Shopcat has it right. The biggest challenge in this industry is that as owners, we terribly lack LEADERSHIP skills. Most everything we complain about has more to do with the guy in the mirror than any external force. "Just wondering how many shops that are having technician staffing problems do any or all of the following: 1. Do you have a recruiting strategy and if so is it effective? 2. Do you have a career path for your technicians? Regular written reviews, regular raises based on those reviews? 3. Do you have a written company policy book and /or a written procedure book? 4. Do you just crisis hire one of the first applicants with a pulse, show them where to park their box and hand them the first work order?" -
It was not like that when I brought it in.
rpllib replied to Hands On's topic in Customer Experience & Reviews
Any chance this is a road hazard issue that could have insurance coverage from their personal auto. Had a similar situation a few years ago and their insurance company bought them a used motor and turbo, even though they were two tracking in a low clearance vehicle when they hit that rock and then tried to drive it home. -
We are just getting started with this. We have google voice on all of our desktops and are able to send texts to customers directly from our desktop via wifi. This started as a result of wanting to be able to text video inspection results to customers via the most convenient method for them. So we are making narrated video of inspection results, uploading them to our dropbox and then sending dropbox links via a text message for the customer to review. We are currently using two wifi enabled s4's(no mobile contract). I struggle asking staff to not use personal cell phones during the day and then turn around and tell them it's ok, just for business purposes. My plan is to put previous generation android or apple smart phones in every employees hands. About $100 a piece on ebay. Next for us is to send customers vehicle completion status updates via text. You can assign a google voice number to every smart phone and actually make and receive calls, texts as well as a variety of email purposes.
- 16 replies
-
- texting
- text messaging marketing
-
(and 1 more)
Tagged with:
-
A recent thread on the subject. Today, I am dealing with a sticking caliper issue with an unhappy customer a year after we did the service. This is definitely a northern teir and above problem(geographically). Since this post we now have attached this to every brake pad replacement and we go over it with every customer. Wish i had it a year ago. A little hard to follow as I have removed the identification of the three other posters. This message was sent by randy lucyk [email protected] Thanks Bob, exactly right. I really don't care if we sell even one more caliper then normal, I just don't want challenges with customers, when it is fairly easily avoidable with the proper conversation. Randy Lucyk Midas, Kalkaska Mi. 231-258-2889 ext. 114 ___________________________________________________________________________ Randy ,I believe it is a necessary evil to prepare the customer for what may or not present itself.All to often we are seen as missing something when high mileage parts fail and they are not recommended by us.we try to decline all recommended parts . I will let our service writers read this and start recommending calipers as preventive maintenance. We have this issue a little more frequently in Canada due to the harsh winters and the sand and salt that is spread on the roads, particularly with phenolic piston calipers. As a rule we explain the possibility of a subsequent failure to the customer and leave the decision up to them. If the vehicle returns with a caliper dragging, the customer is already aware of what has happened and due to the information given to them, generally understand the situation. I think if the customer is armed with the knowledge to make an informed decision is sufficient. This knowledge also gives the customer some peace of mind, I have had customers come back, already knowing what has happened and what it will take to repair and they are rarely upset with the shop. A disclaimer may be prudent although I'm not sure it is necessary of the condition is explained correctly. > > I like the disclaimer, however, I believe it is a bit lengthy. The longer it is, the more guilty it sounds/appears, to me. It's a great CYA tactic that I don't see a downside to. It will force the conversation, resulting in either a sale or at least advanced warning. Plus it will serve as your paper trail should they need to come back. > > I will be adopting this idea/approach to better serve my customers and better protect us. > > > This message was sent by randy lucyk [email protected] > > Probably only an issue for a 1/3 or so of the stores in the system(northern tier). As previously discussed we occasionally have issues with caliper failure after brake repairs where we believe no defects were evident at time of pad replacement, yet a caliper will come back dragging with no external issue. This is not a pin or hardware issue. It is unlikely any shop is much better than we are at cleaning and lubing with synthetic lube. > > Had a conversation recently on the subject with a veteran dealer who strongly suggests caliper replacement on 3rd pad replacement or greater. In other words, the vehicle has gone thru the original brakes and one replacement set and is now in for it's third set of brake pads. He uses the lifetime warranty as a trigger(2nd set of pads were done in the system and now in for warranty repairs) for his stern caliper recommendation. > > This got me to thinking. We have no MAP guideline for making such a stern recommendation, so what do we base it on? My mind went to considering what other services might cause us to make suggestions, even strong suggestions with no industry basis. Timing belts came to mind immediately. At least in our store, we might consider replacing just the belt at it's first interval, but would would not even agree to do the work if it was not getting a complete timing belt kit by the second interval. More recently TPMS reseals are handled at our store the same way. We might do a new set of tires at 60k without a reseal, we will always strongly suggest at the next tire replacement. > > So we have this issue with calipers that is not consistent or very common. What do we do, to prevent unhappy customers. I offer this for your consideration: > > "Brake caliper discussion. High mileage vehicle and/or 3rd(or greater) set of brake pads being installed at this time. > As discussed, we are about to install what is likely the third set of brake pads(or greater)on your vehicle, while reusing what appear to be the original brake calipers. The brake calipers on your vehicle have been visually inspected for external signs of defects and the components retracted correctly with normal effort and approved tools and procedure. No detectable defects have been noted at this time. It is not possible to determine internal caliper defects during normal brake service. Internal defects are generally the cause of caliper > related brake issues, where no external defect is evident. It should be noted > that internal failure of at least one caliper is possible prior to the brake pads being installed today becoming worn out. Occasionally that failure can occur fairly soon after recent brake pad replacement, even though no detectable issue was evident at time of replacement. Internal failures of the brake calipers that were undetectable at time of service will result in additional cost and inconvenience, even if failure occurs shortly after pad replacement." > > To be attached to all brake pad replacement labor entries and deleted from low mileage brake replacements. > > Wordy for sure, this is version 4. At minimum, it will require service advisors to have the conversation. > > Overkill? Yea? Nay? Thief? Crook? Brilliant? Scare tactic? > > All comments are appreciated > > Randy Lucyk > Midas, Kalkaska Mi. > 231-258-2889 ext. 114